The production capacity of a meltblown nonwoven fabric machine is determined by several factors, including:
Machine Size and Configuration: The physical size and configuration of the machine play a significant role in determining its production capacity. Larger machines with more extensive production lines generally have higher capacities compared to smaller machines.
Number of Spinnerets: The number of spinnerets, which are small nozzles through which the molten polymer is extruded, affects the production capacity. Machines with a higher number of spinnerets can produce more fabric in a given time, increasing the overall capacity.
Extrusion Rate: The extrusion rate refers to the speed at which the molten polymer is forced through the spinnerets. Machines capable of higher extrusion rates can produce more fabric per unit of time, resulting in higher production capacity.
Line Speed: The line speed refers to the speed at which the fabric is formed and collected after being extruded through the spinnerets. Machines with higher line speeds can produce more fabric within a specific timeframe, increasing the production capacity.
Process Efficiency: The efficiency of the meltblown process, including factors such as polymer melt temperature, air velocity, and stretching mechanism, can influence the production capacity. Optimized process parameters can result in higher productivity and improved fabric quality.
Material Properties: The properties of the raw materials used, such as polymer type, melt flow rate, and viscosity, can impact the production capacity. Some materials may require specific processing conditions that may affect the machine’s speed and overall capacity.
Operator Skill and Experience: The skill and experience of the machine operator can also contribute to the production capacity. A well-trained operator who understands the machine’s operation and can optimize the process parameters can help maximize the machine’s productivity.
It’s important to note that the production capacity of a meltblown nonwoven fabric machine is not solely determined by a single factor but is a combination of various factors working together. Manufacturers provide specifications and guidelines that indicate the estimated production capacity of their machines based on these factors.
What are the key steps involved in the operation of a meltblown nonwoven fabric machine?
The operation of a meltblown nonwoven fabric machine involves several key steps. Here are the general steps involved in the process:
Raw Material Preparation: The first step is to prepare the raw materials. meltblown nonwoven fabric machine This typically involves melting and filtering the polymer material to ensure it is free from impurities and has the desired properties for meltblown fabric production.
Polymer Extrusion: The filtered polymer material is then fed into the extruder of the machine. meltblown nonwoven fabric machine Inside the extruder, the polymer is melted and pressurized to a specific temperature and viscosity suitable for the meltblown process.
Filament Formation: The molten polymer is forced through spinnerets, which are small nozzles with tiny holes. As the polymer is extruded through these spinnerets, it forms extremely fine filaments. The spinnerets are designed to create a specific filament diameter and arrangement.
Quenching and Cooling: After the filaments are formed, they are immediately subjected to a high-velocity airstream called quenching air. The quenching air rapidly cools the filaments, solidifying them into fine fibers.
Fiber Collection and Formation of Web: The solidified fibers are collected onto a moving conveyor belt or drum called a collector. As the fibers accumulate, they form a web of randomly oriented fibers. The web may undergo additional processes such as compaction or bonding, depending on the desired fabric characteristics.
Finishing Processes: Once the web is formed, it may undergo various finishing processes to enhance its properties. This can include treatments such as heat setting, calendaring, or applying chemical finishes to improve strength, stability, or other specific properties.
Winding and Cutting: The final step involves winding the produced meltblown fabric onto rolls. The rolls can then be cut into desired lengths or widths, depending on the application requirements.
Throughout the operation, the machine’s control system monitors and adjusts various parameters such as temperature, air velocity, line speed, and tension to ensure consistent and optimal fabric production.
It’s important to note that the specific steps and processes may vary depending on the design and configuration of the meltblown nonwoven fabric machine and the desired fabric specifications.
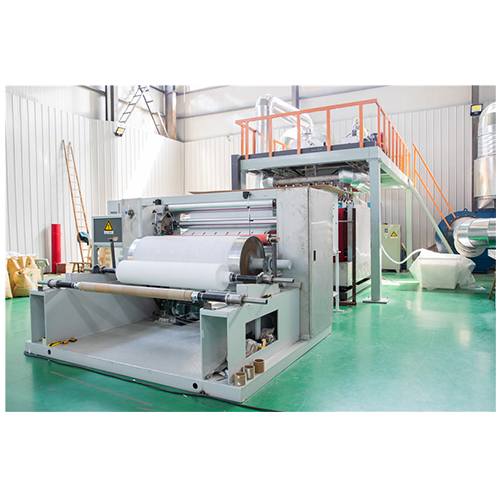